Introducing QHUB
Learn how our QHUB Dashboard streamlines document retrieval, service requests, and more...
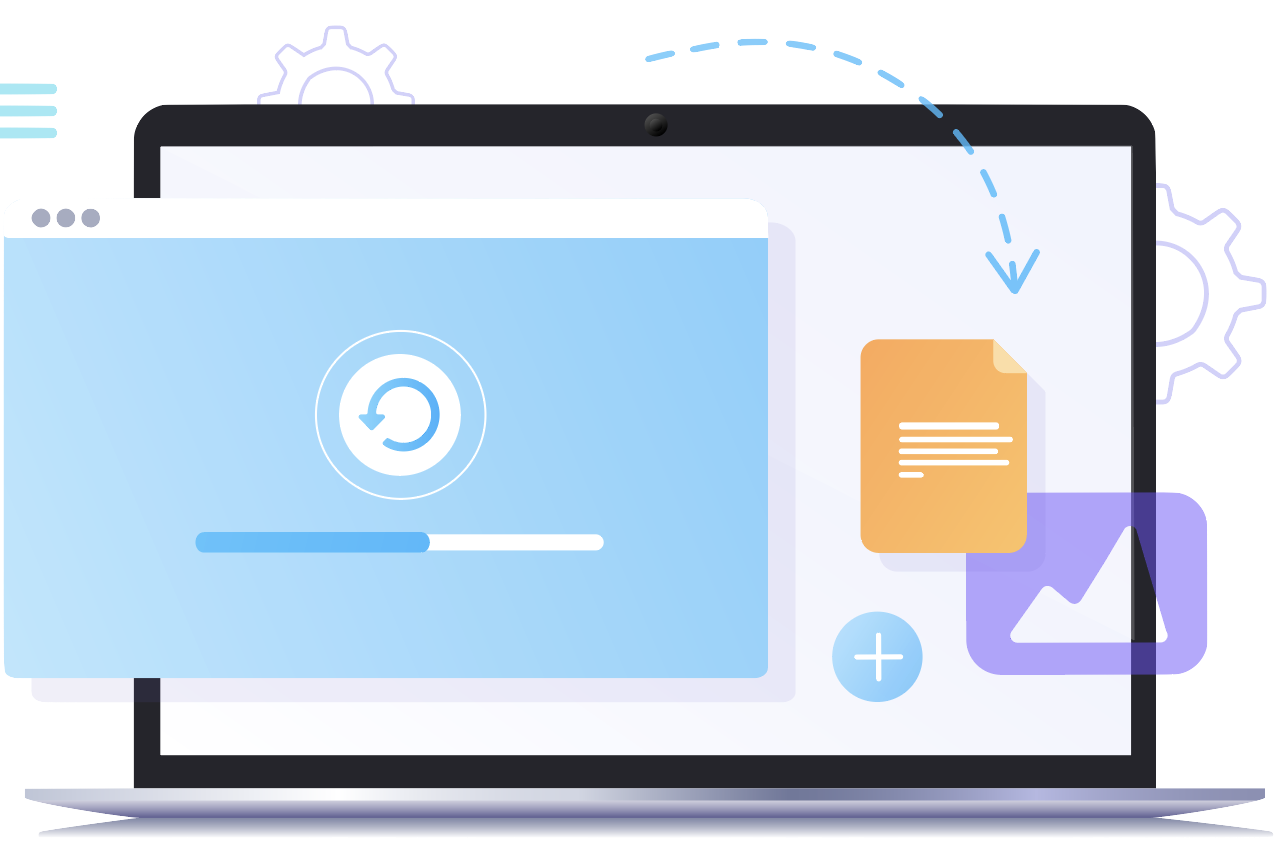
Learn how our QHUB Dashboard streamlines document retrieval, service requests, and more...
Autoclaves are essential for sterilization in life sciences, but improper validation can lead to regulatory violations, product recalls, or compromised safety. Our autoclave qualification services verify that your equipment consistently meets performance standards, ensuring:
Compliance with GMP, FDA, and USDA APHIS regulations.
Reliable sterilization for pharmaceuticals, medical devices, and hospital equipment.
Reduced risk of contamination in biotech and pharmacy settings.
Our nationwide team ensures seamless execution, whether you're in a small pharmacy or a large-scale manufacturing facility.
At Quantus, we provide expert autoclave validation and qualification services tailored for pharmaceutical, biotech, medical device, hospital, and pharmacy sectors. Our validation services ensure your sterilization equipment meets stringent GMP, FDA, and USDA APHIS standards, protecting both compliance and product integrity.
Expertise: Over 20 years serving life sciences with GMP and FDA expertise.
Speed: Reports delivered in 2 weeks, minimizing operational delays.
Nationwide Service: Supporting facilities across the U.S., including the mid-Atlantic region.
Regulatory Compliance: Aligned with ISPE, ASTM, and OEM standards for complete validation assurance.
Our experienced engineers implement proven IQ, OQ, and PQ protocols to thoroughly validate your autoclaves, delivering detailed reports to minimize operational downtime. Having supported life sciences clients nationwide for over 20 years, we've earned trust through our expertise and commitment to quality—from small labs to large-scale manufacturing facilities.
Ready to ensure your autoclaves are fully compliant? Request a quote today and let Quantus handle your autoclave validation needs with confidence.
In the life sciences industry, "validation" and "qualification" are closely related but distinct terms, often used interchangeably.
Qualification refers to the specific, documented steps—Installation Qualification (IQ), Operational Qualification (OQ), and Performance Qualification (PQ)—that verify an autoclave meets predefined standards. IQ ensures proper installation and supporting utilities (e.g., steam, water, air). OQ confirms the autoclave operates correctly under specified conditions, often with empty chamber runs. PQ tests the autoclave’s performance with loaded chamber runs, using various load patterns (e.g., dense packs, mixed instruments) to simulate real-world use.
Validation is the broader process that encompasses qualification, ensuring the autoclave consistently delivers compliant sterilization over time. This includes not only IQ, OQ, and PQ but also cycle development (optimizing sterilization parameters like time, temperature, and pressure), validation of supporting utilities, and ongoing monitoring to confirm reliability. For example, validation might involve testing multiple load configurations and ensuring the autoclave’s cycles meet GMP and FDA standards across repeated runs.
At Quantus, our autoclave validation and qualification services cover the full spectrum—qualification steps, cycle development, and comprehensive validation—to ensure your equipment is compliant and reliable for pharmaceutical, biotech, medical device, hospital, and pharmacy applications.
At Quantus, the on-site qualification phase—covering Installation Qualification (IQ), Operational Qualification (OQ), and Performance Qualification (PQ)—typically takes 3–5 days, depending on the number of autoclaves and facility complexity. This includes setup, empty chamber testing, and initial loaded chamber runs to verify performance.
The broader validation process encompasses more extensive testing, such as multiple cycle runs, various load patterns, cycle development, and supporting utilities like clean steam qualification. Depending on the rigor of testing and any issues like failed runs, validation can take 2–4 weeks. For example, clean steam testing, as per ISPE guidelines and EN 285 standards, may require additional time for sampling and analysis to ensure steam quality. Once testing is complete, biological indicators are analyzed in our microbiology lab in Blue Bell, Pennsylvania, where we address any deviations with customer approval.
After all testing, data QA review, and final signatures are completed, Quantus delivers the final report—a comprehensive binder with the completed protocol and all related data—within 2 weeks, ensuring your facility meets GMP and FDA compliance with minimal downtime.
I am very pleased with the services provided. The technicians are exceptional to work with, and the customer support team is incredibly responsive and accommodating. The pricing offers excellent value for the services provided.
Century Therapeutics Drew
The technicians here do an outstanding job. I truly appreciate the responsiveness of the customer support team and their proactive approach to scheduling.
Ellume Ken
Everything is going great with the services. The technicians are top-notch – professional, honest, and very solid in their work. They provide excellent communication and feedback.
RegenXBio Blake
Working with Quantus to resolve the disorganization of previous 3rd party reports. I have received positive feedback on the work Quantus is doing. We're looking forward to a meeting with the top management and business development teams to gain more feedback and develop additional controls.
Christiana Care James
Ensure optimal sterilization, verifying low non-condensable gases, superheat, optimal dryness, and clean steam to meet stringent healthcare standards.
Stay compliant with our routine Autoclave Calibration Services every six months, ensuring accuracy and reliability between re-qualification periods.
Nationwide commissioning, qualification, and validation services for life science lab equipment, manufacturing facilities, and controlled storage.